Operation Project Burger
In recent years, AWB Engineers has seen an increased demand to repurpose existing warehouse space into food processing and distribution facilities. Recently, AWB Engineers was hired to convert an existing warehouse located in a business park in Atlanta, Georgia into a food processing center for a nation-wide fast-food chain. Our task was to design various civil/site, structural and MEP systems needed to transform the existing warehouse shell into a state-of-the-art food processing facility. The AWB team of engineers and architects surveyed the existing facility to determine what modifications would be required in order to comply with USDA guidelines for this new food processing facility.
Architectural or Structural food processing requirements
After a comprehensive review of the existing structure, AWB Engineers identified the roof and floor systems as being inadequate and would require significant structural modifications. These items are extremely critical to consider and to plan for in advance. A typical warehouse roof is generally designed for much lighter loading than a food processing facility and would not be structurally adequate to support the loading imposed by the new mechanical, electrical, and plumbing systems. In addition to strengthening the existing roof, a dedicated steel structure was designed to support the hygienic CPA units serving the food processing areas.
The existing floor slab, originally designed for warehouse use, was not adequate for food processing. The floors were not sloped and did not have floor drains that would now be required for sanitation. At the refrigerated spaces, the new floor system was designed to prevent frost build up in the soil under the freezer. As a result of the extensive slab modifications that were needed, AWB Engineers’ recommendation was to have the existing floor slab demolished and replaced with a new slab that would be detailed with the proper slopes, drains, and thermal insulation required.
Aspects of the thermal envelope of this new refrigerated building were addressed by specifying thermally efficient insulated dock doors, wall and ceiling panels, in addition to the floor slab modifications previously mentioned. Stainless steel wall and ceiling finishes were specified to ensure that the building will withstand rigorous daily caustic sanitation requirements. To protect the insulated wall panels, concrete curbs were installed at the base of the wall panels. This detail is essential in areas where forklift and pallet jack traffic is expected.
Proper Refrigeration for food processing facilities
A critical aspect of every refrigerated food processing facility is a proper refrigeration system. The refrigeration system design incorporates a critical process air systems (CPA hygienic units) that allows maintaining required temperatures, humidity adjustment, sufficient ventilation and contaminant filtration. The CPA unit is also used for daily cleanup mode in order to dehumidify the air and remove any potential of condensation during the production.
Plumbing, Electrical and HVAC systems that are suitable for food processing facilities
Upgrades to the utility systems were an essential part of the transformation from a dry warehouse into a state-of-the-art food processing facility. The existing electrical, water and HVAC systems were insufficient for the increased demands of the new facility. We designed a new electrical service coming into the building by replacing the transformer, switchgear, and side panels. We also upgraded the domestic water service and the process waste capabilities in the building.
A food processing facility should be designed and detailed with cleanliness and sanitation in mind. Ideally, the MEP systems should be installed above a “walkable” ceiling and routed vertically down into the clean/sanitized spaces below, minimizing horizontal surfaces that allow dirt or dust to settle on over time. This also allows for routine maintenance on the utility systems to be performed within the interstitial space above the processing rooms, and not in the sanitized space below the ceiling.
There is much to consider when converting a typical warehouse building into a USDA compliant food processing facility. With these types of building transformations, it is extremely critical to examine and execute a detailed plan that addresses the various system modifications that will be required. At AWB Engineers, we take pride in providing our clients with quality design solutions tailored to the food and beverage industry.
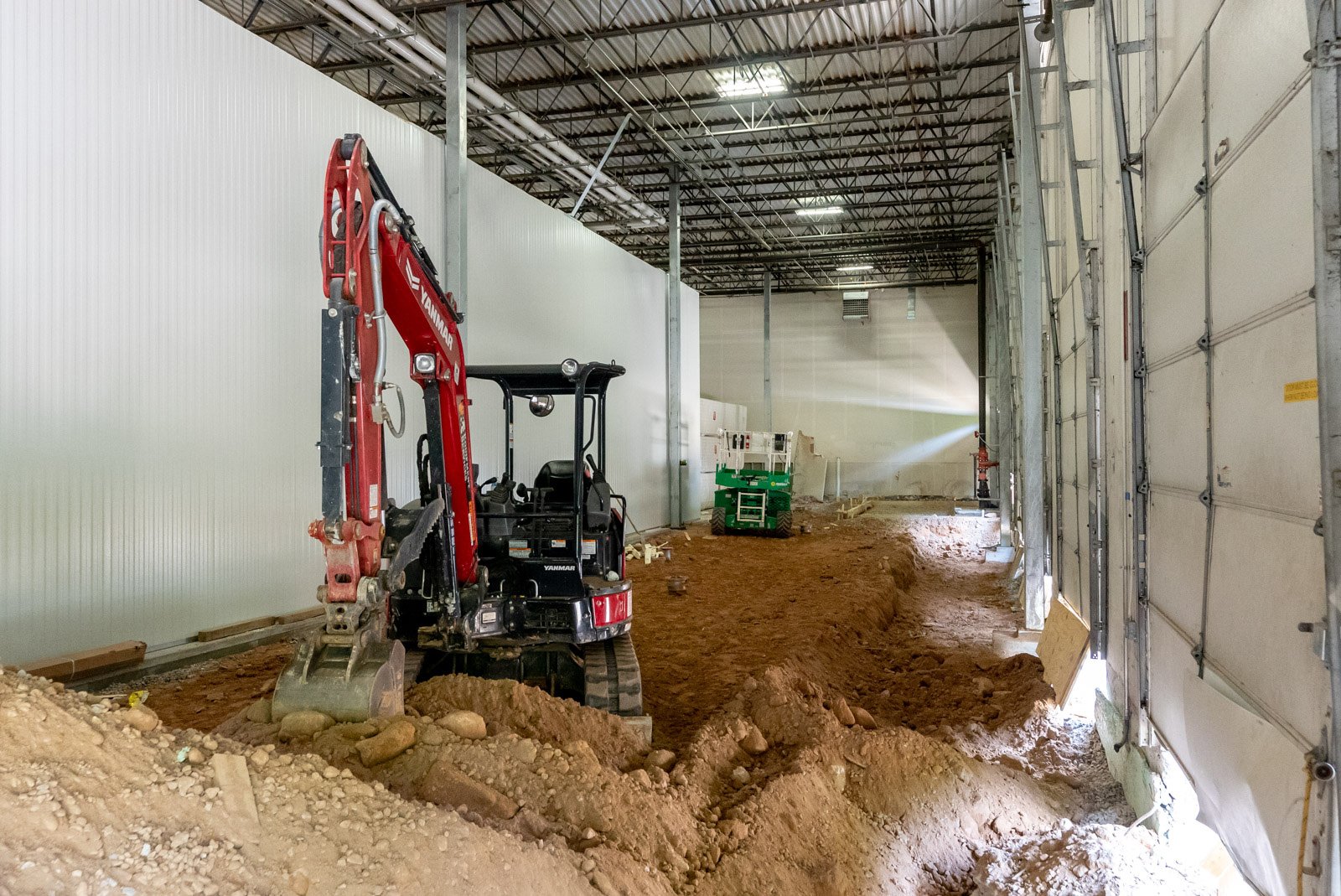
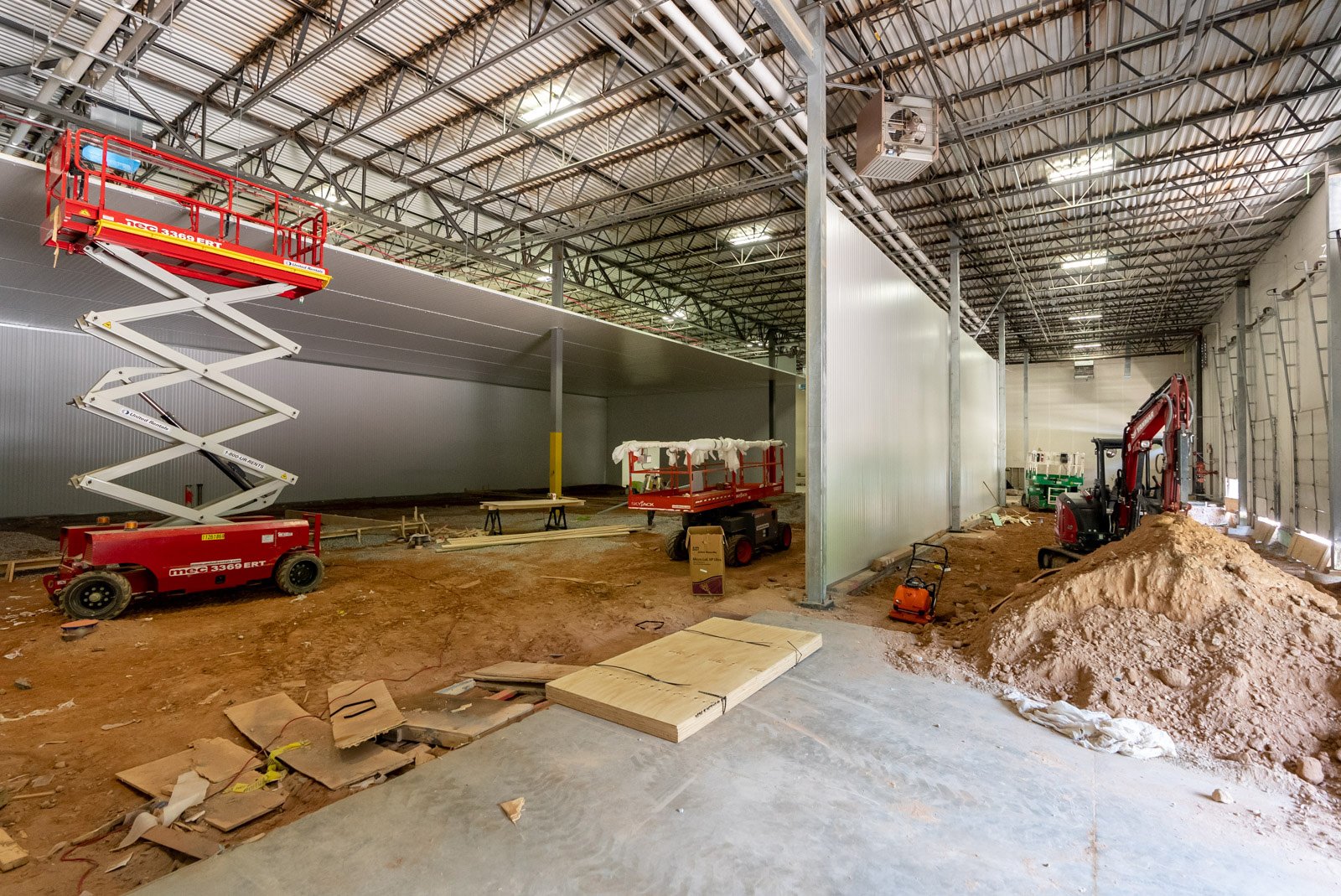
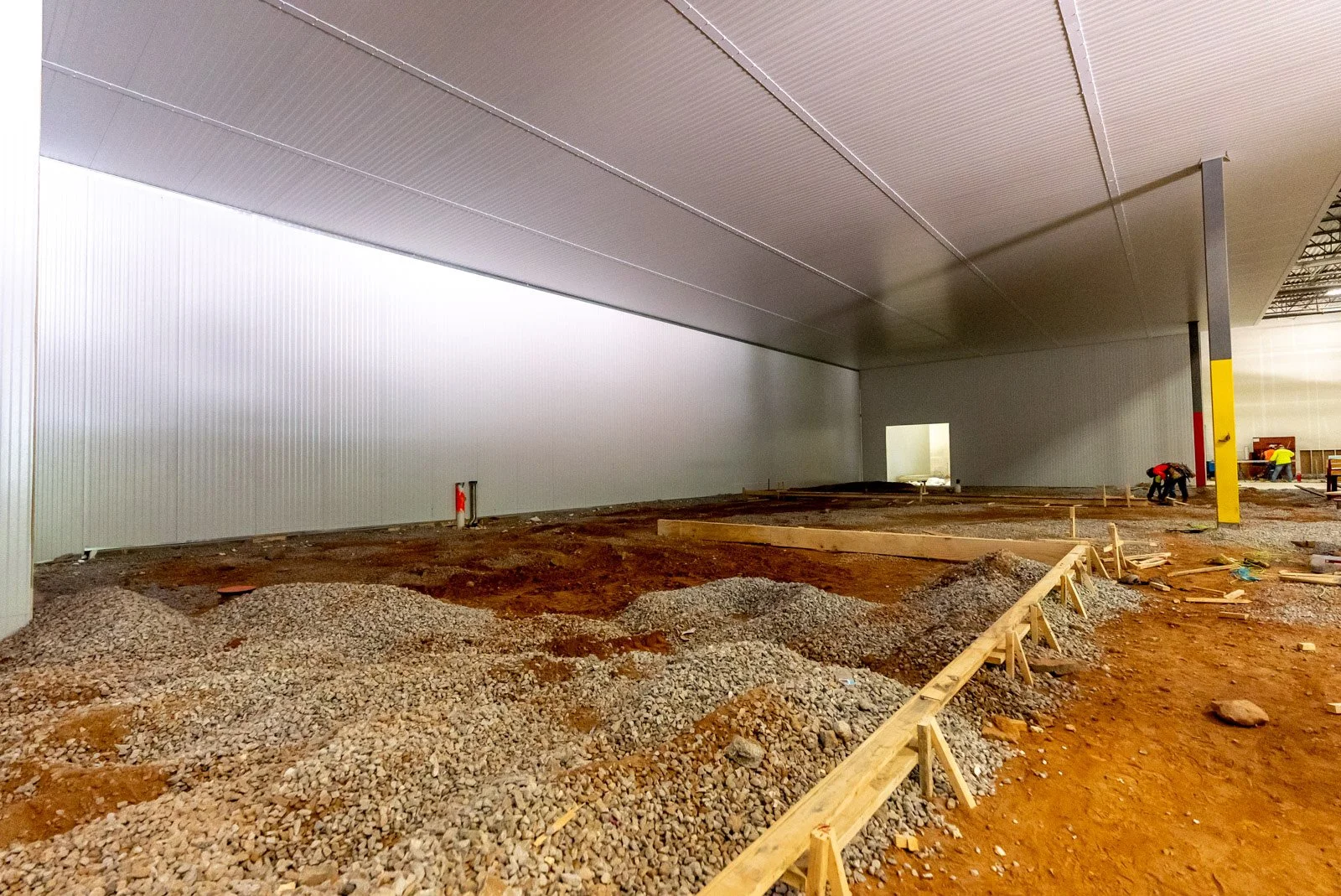
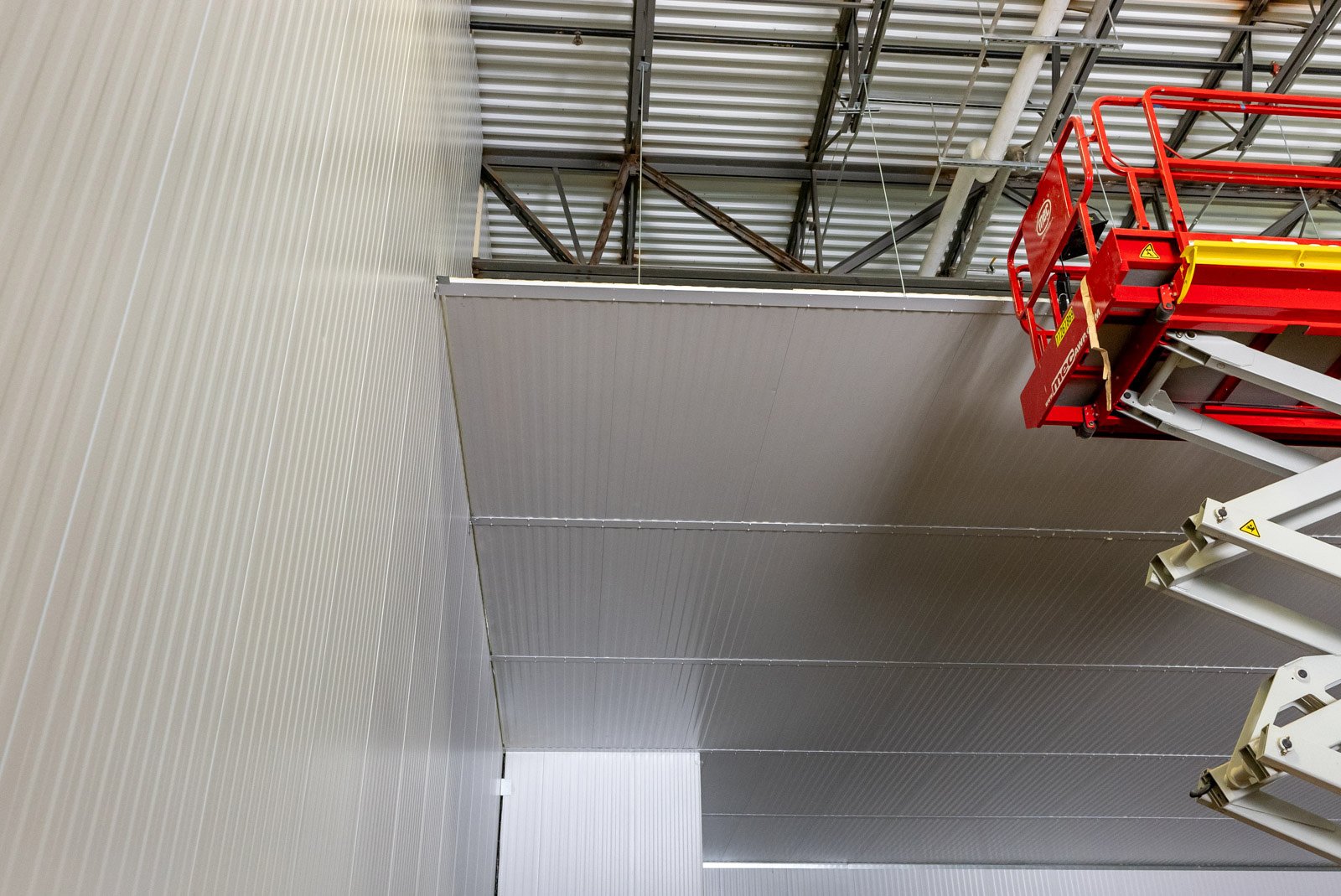
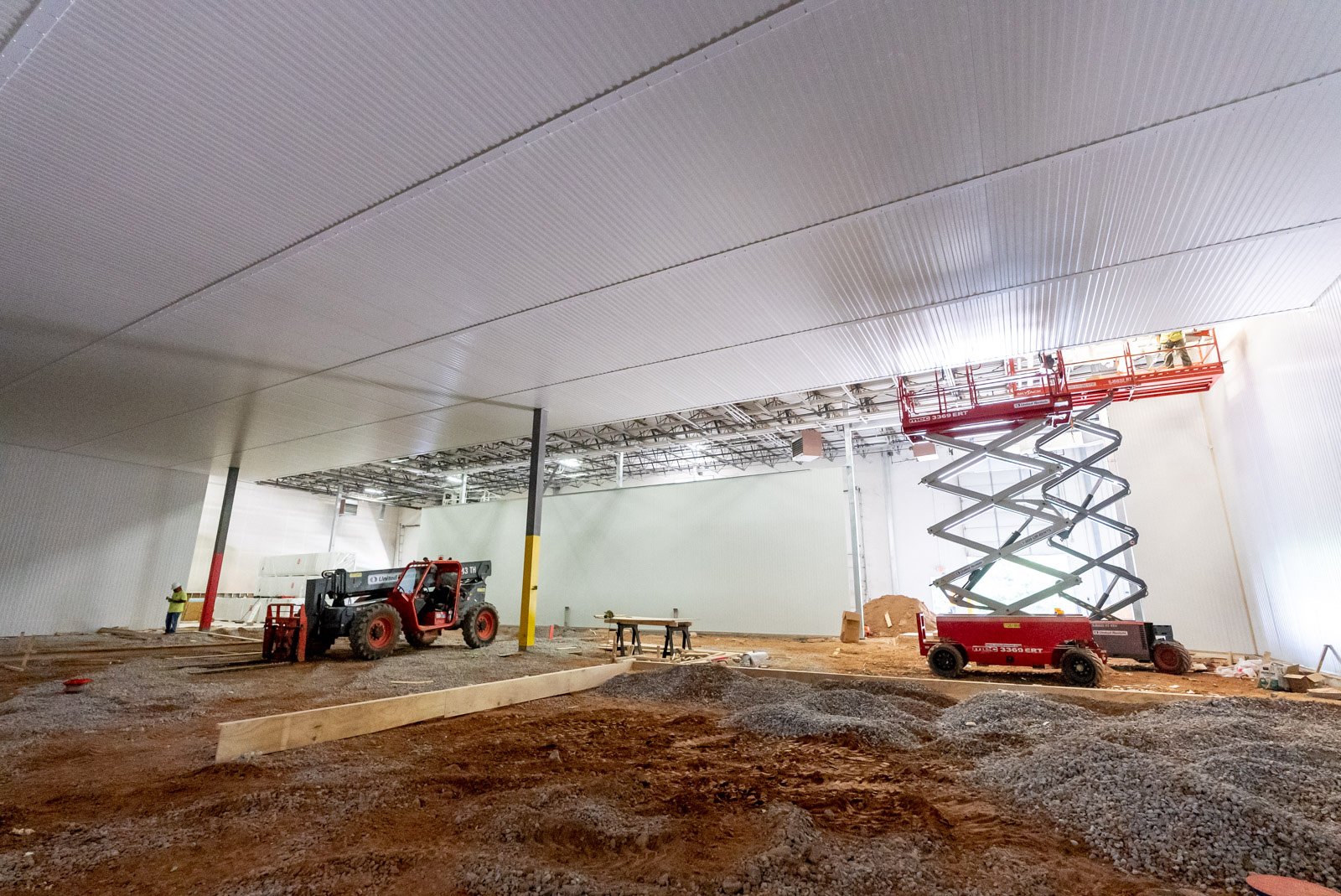
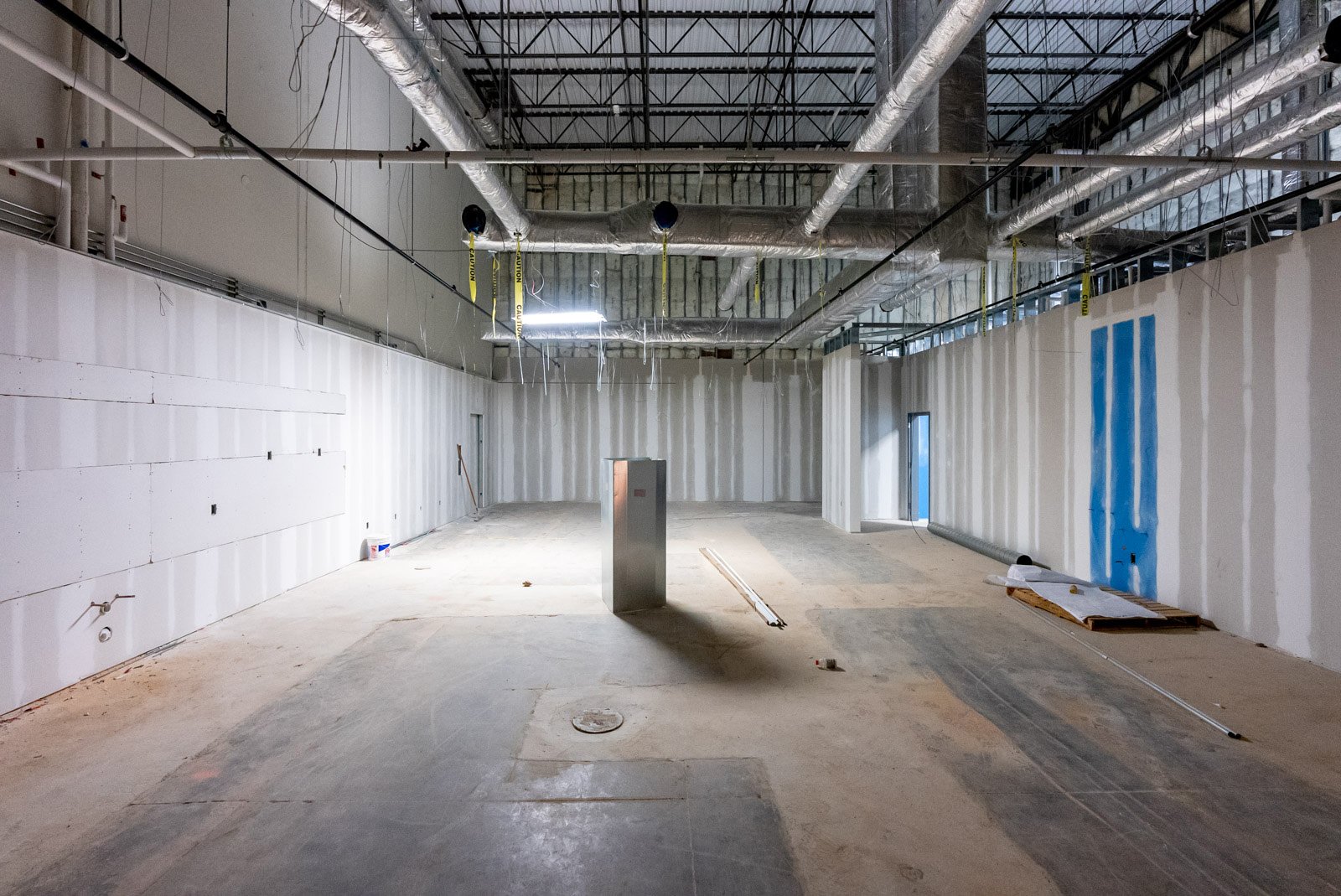
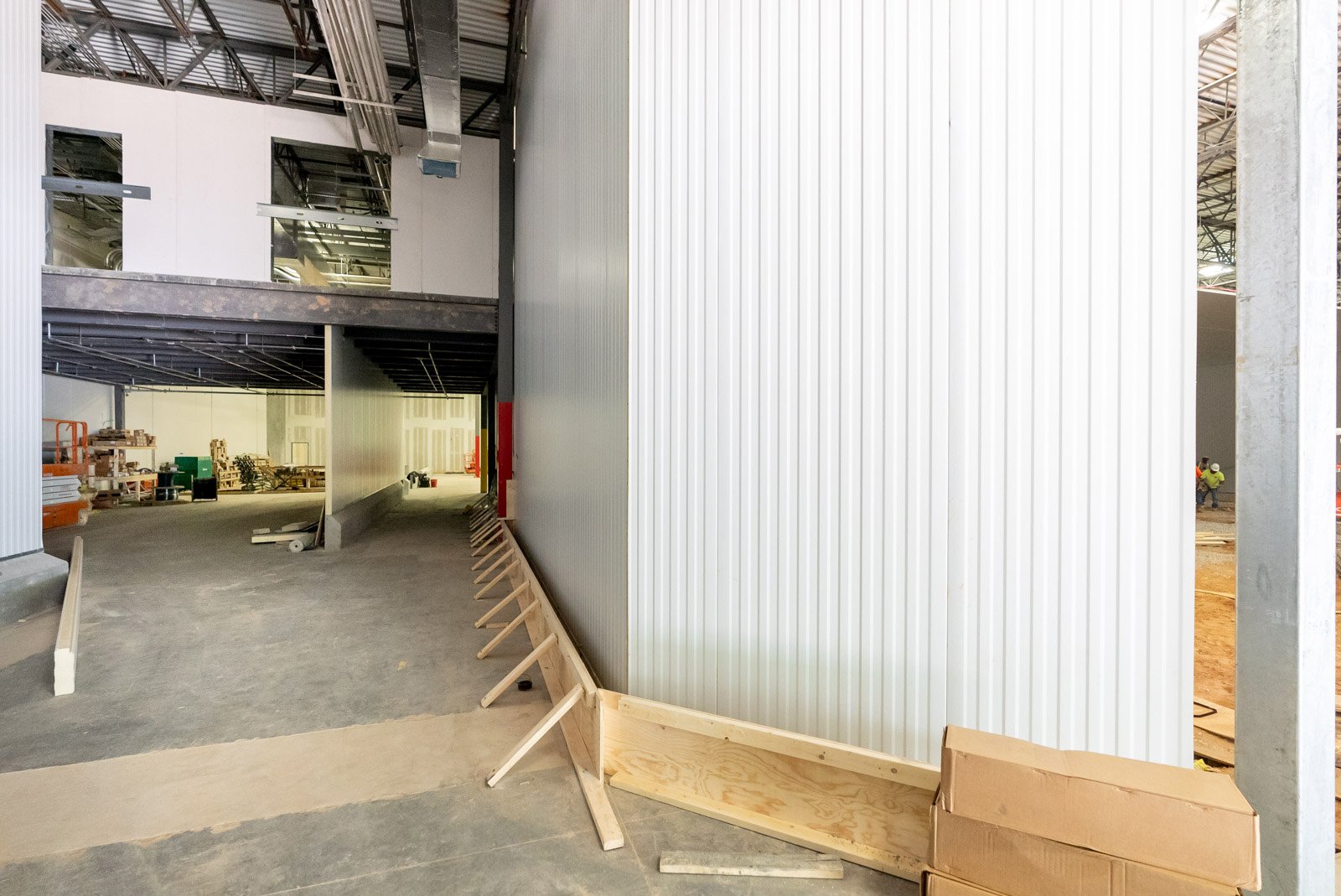
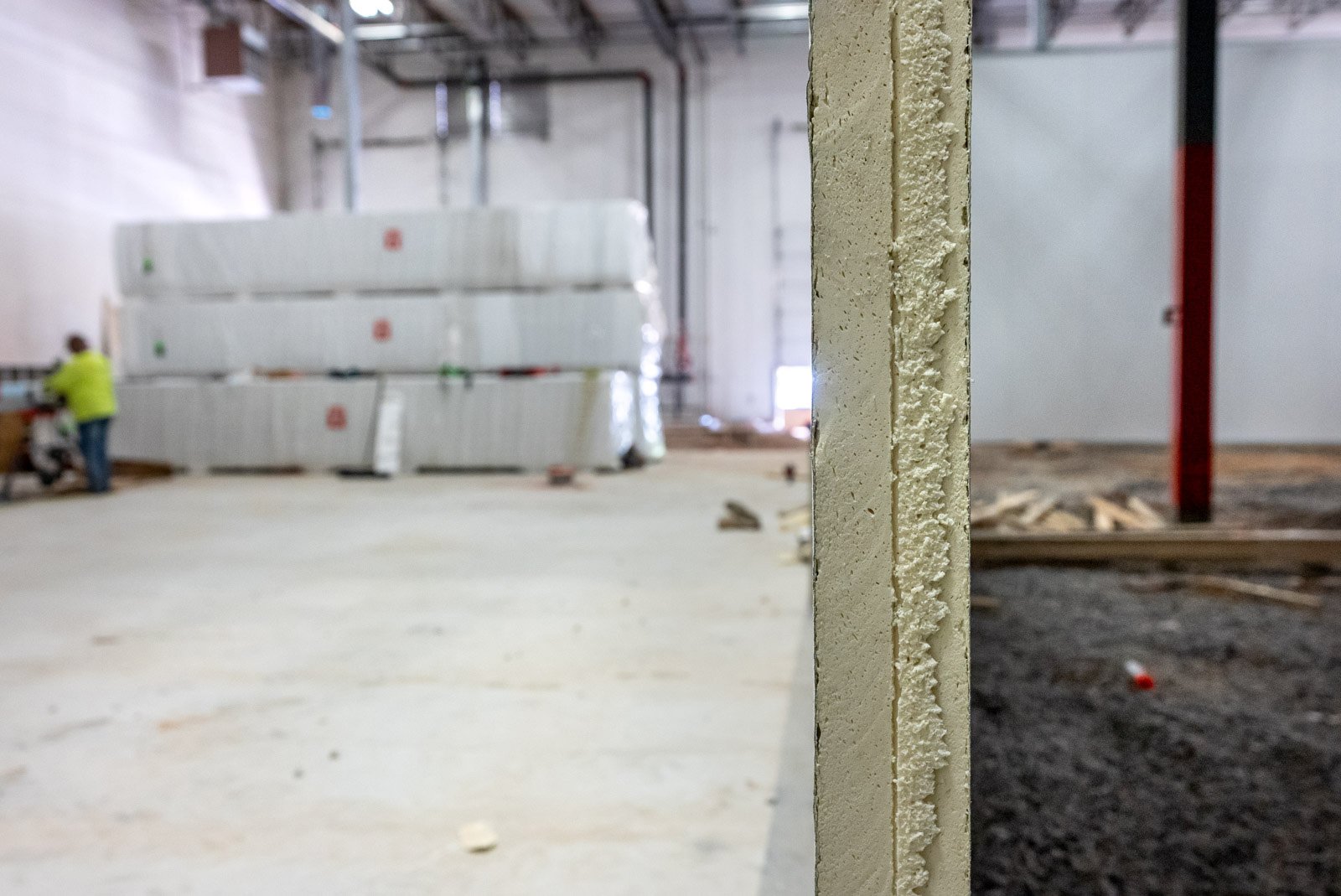
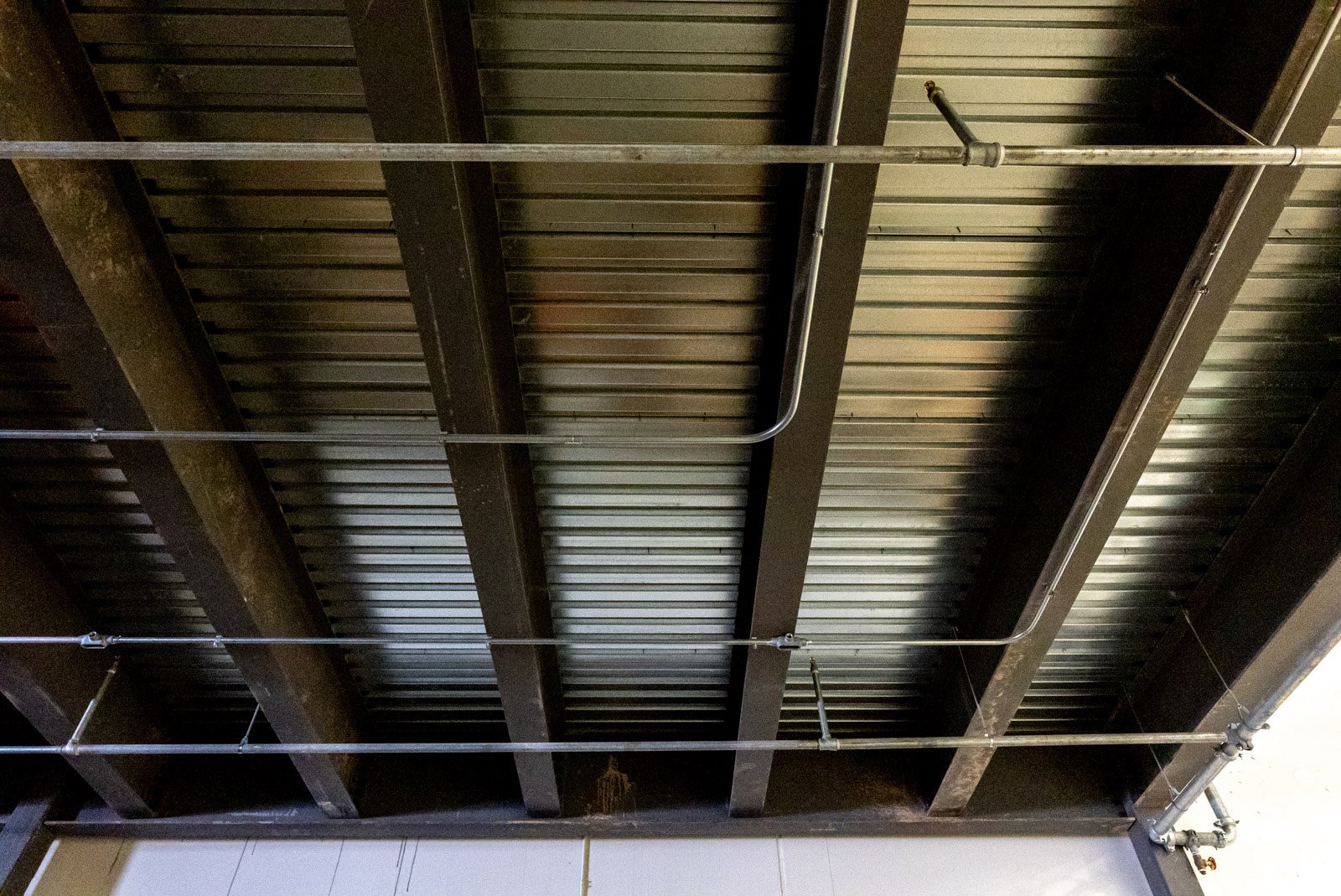
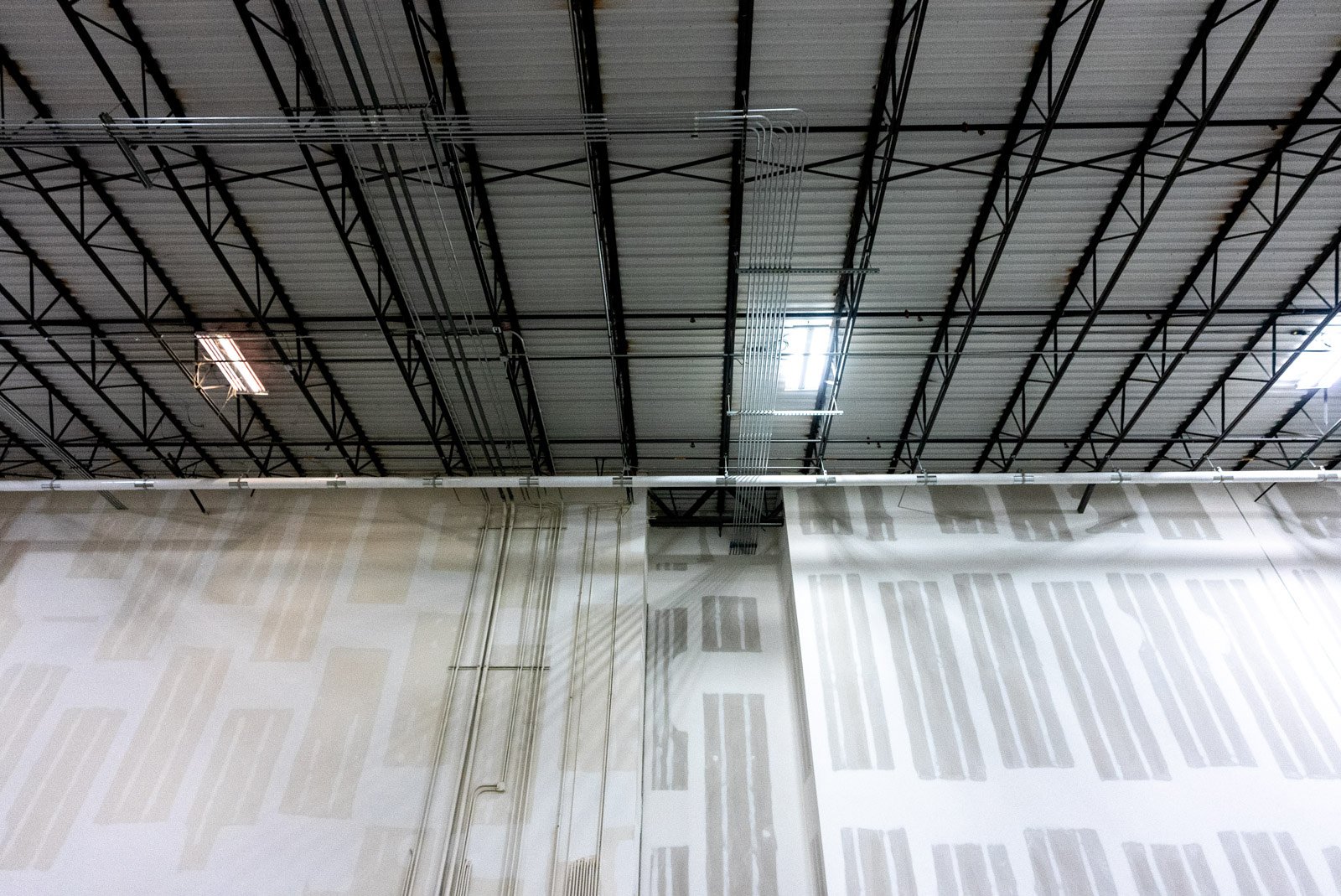
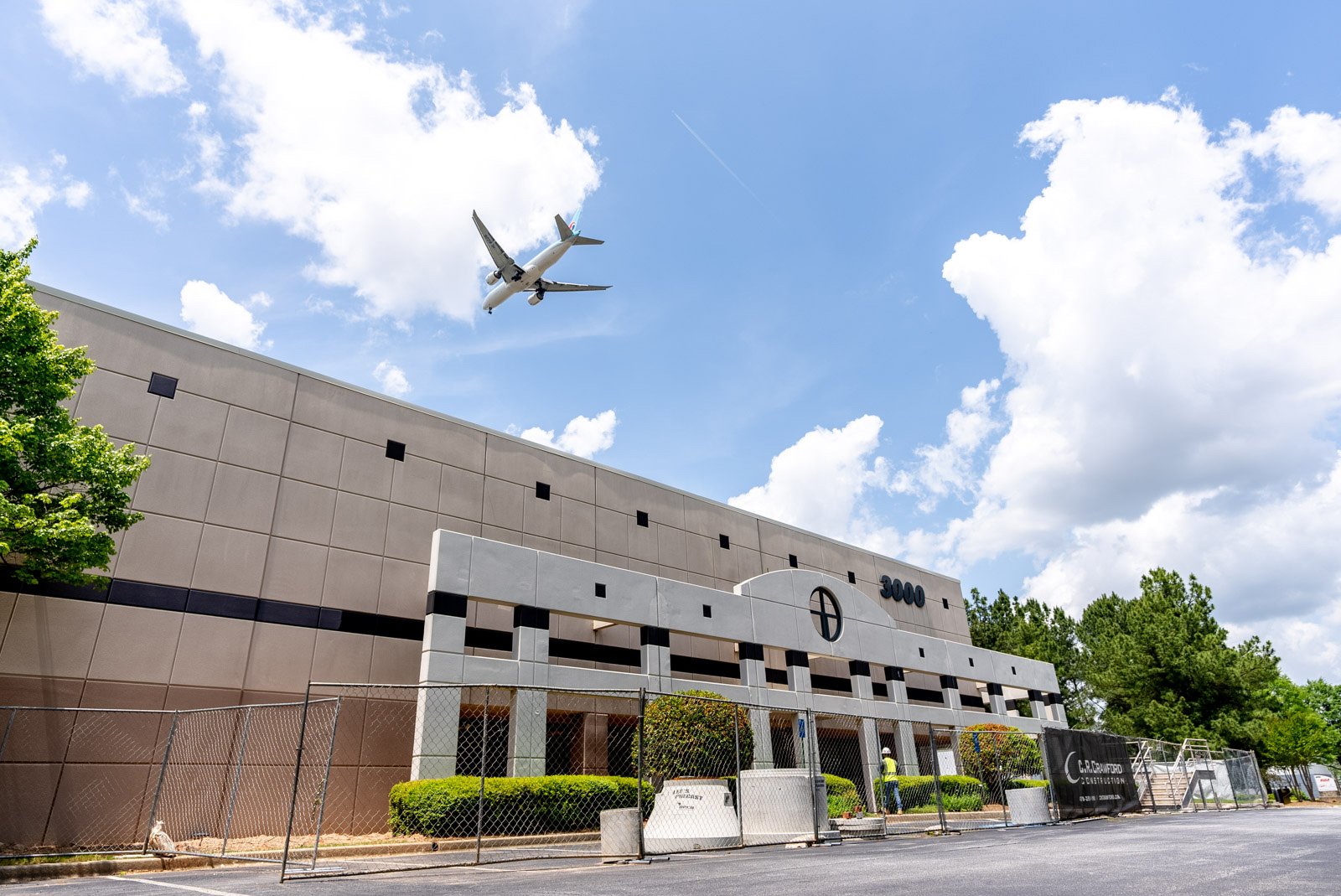